The number one question we get from customers is: “What is the accuracy of your measurement system?“
The intent behind the question is correct – but the question is not the right one. What you really want to know is: “This is the part I am producing, and these are the things I need to measure – can you solve my problem?”
And accuracy is only one small part in determining whether we can. Let’s discuss what you should be asking instead to better understand if we’re the right provider for you.
Accuracy – and why it’s usually the wrong question to ask
Our everyday use of the term accuracy tends to deceive us. Accuracy within the context of measurement systems never consists of only one value and always depends on the context. It’s only one part of the equation that determines measurement variation.
In other words, our answer to the question: “What’s your system’s accuracy?”, will always be “it depends”. And that’s likely not the answer you want to hear. So how can we get closer to the answer you’re looking for? What do measurement variations depend upon?
In the simplest sense, a measurement can be accurate, while not being precise. It can also be precise, without being accurate. To have the lowest variance in measurement, it needs to be both accurate and precise.
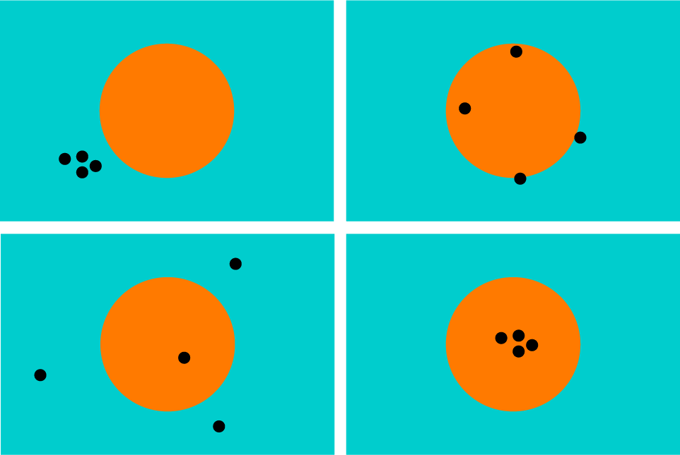
Example 1
The problem is, that you cannot put singular numbers on either accuracy or precision. So we need further sub-variables for each variable, that can quantify the other relevant dimensions they consist of.
In a theoretical sense, measurement variation can be said to equal bias plus repeatability. So the average of multiple, repeated measurement values in relation to the reference value.
In a real-world inspecting scenario, however, you rarely run measurements only at one point in time on a single, unique part. This means we need to introduce even further variables that can quantify space and time. Linearity and reproducibility quantify the level of measurement variation across different locations and parts.*
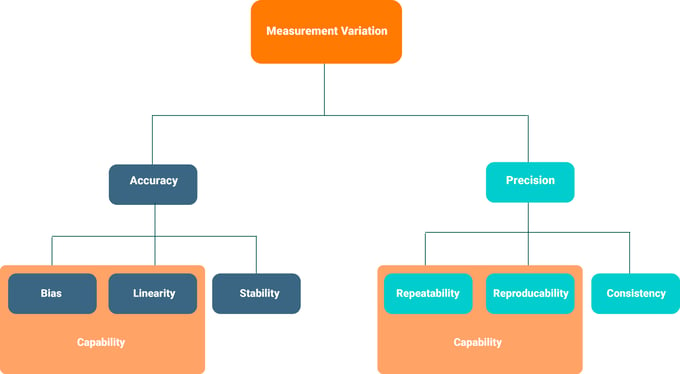
Example 2
A measurement system’s capability is a term that is used to describe how likely the system is to measure within the same amount of variation across multiple similar, but naturally slightly different parts. It is a function of a system’s measurement variation, derived from its bias, linearity, repeatability, and reproducibility.
With the number of sub-variables that need to be introduced, it quickly becomes apparent that accuracy is not the right question to ask. It is already significantly more meaningful to ask about a system’s capabilities than its accuracy.
But there’s still one more important distinction to be made before arriving at the correct question.
System capabilities vs Process requirements
There are two levels to the question you should be asking to determine whether a particular inspection solution solves your problem.
The first level is a question of what was discussed above: does the measurement system have the capability of measuring your parts?
The second level has less to do with the measurement capabilities of the system, and more to do with your ways of working: does the measurement system fit your process requirements?
This is where things get particularly tricky. You might specifically need an in-line solution. You might need a solution that can produce the same results under different temperatures. The level of automation, the physical size of the solution, the technical setup guidance, the required inspection speed… The list of possible variables is almost endless.
Naturally, some variables matter a lot and then some variables barely matter at all. That’s why it’s important to define these as best as you can. And that brings us to tolerance levels.
The question you should be asking is: What are the tolerance levels?
You’re not getting a measurement system for the sake of getting a measurement system. You’re not even getting one to measure parts as accurately as you can. You’re getting a measurement system to ensure your parts reach certain requirements – whether mandated by law, required by customers, or upheld by your high standards.
These certain requirements inform your tolerance range. It’s important to approach this from a top-down perspective, thinking about the kind of part you are manufacturing, and which tolerances are correct for that specific part. Tighter tolerances don’t automatically translate into higher-quality parts. It’s finding the correct tolerance level that creates a high-quality part.
As such, at Mapvision we believe that the question you should first be asking solution providers is this:
“Is your measurement system capable of inspecting this item on our production line within this level of tolerance?”
This question covers the two levels of system capability and process requirements. It allows you to weigh the measurement uncertainty of the system against your tolerance requirements, and see whether the solution will improve your production.
In other words, the question asks: “This is the part I am producing, and these are the things I need to measure – can you solve my problem?”
That’s where every meaningful conversation starts in our experience. It’s not only about accuracy. It’s not only about system capability. It’s not even only about your process requirements. The inspection process is full of intertwined variables, and we help you identify, evaluate, and solve the ones that are proving to be problems for you.
If you want to map out your process requirements and see whether Mapvision is right for you, book a consultation call with one of our experts. We’ll help you evaluate whether our inspection solution can solve your production problems.