Mapvision Care
Service programs for Mapvision inspection systems, tailored to your specific needs whether it is agility, early response, or support for your in-house system managers and maintenance teams.
Standard Program
For mature manufacturing lines that do not require frequent adjustments and feature modifications. In addition to standard online support without delay and troubleshooting via remote connection, the Standard program covers an all-around annual maintenance and system calibration on-site by a visiting Mapvision expert to ensure accuracy and precision.
Extended Program
For early stage production lines and manufacturing programs that require agility with frequent engineering changes and feature modifications. The Extended program covers all inspection modifications you require for your changing in-line inspection needs such as new feature additions—avoiding additional, separate costs.
Light Program
For mature manufacturing lines with in-house maintenance teams. The Light program cuts service costs by excluding the annual maintenance service by a visiting Mapvision expert. You can instead train your own maintenance teams by separately purchasing a training program. However, the annual system calibration and certification should still be performed by a Mapvision expert. It can be purchased separately.
"The best support group I've worked with during my 30 years in this business."
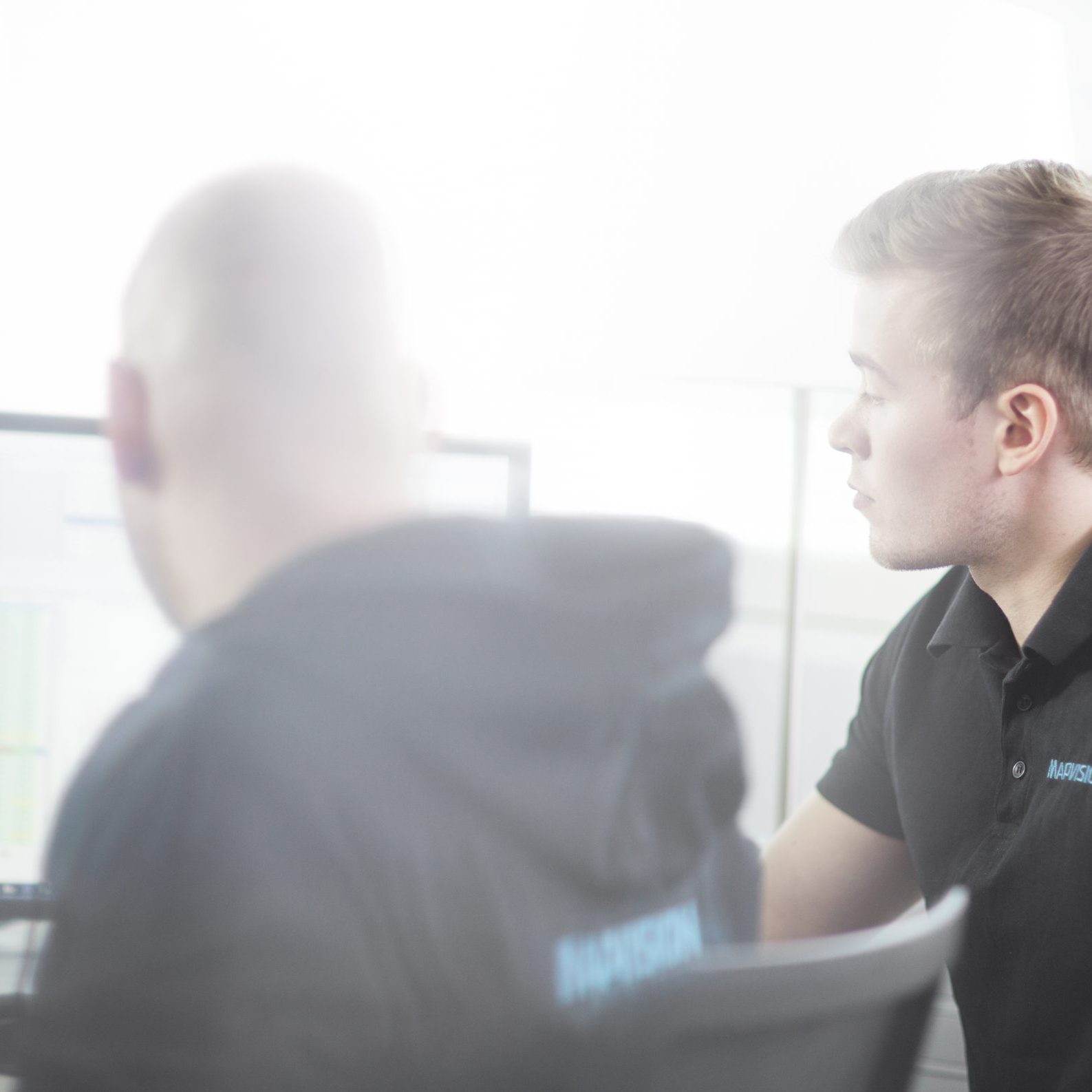
Online Support & Remote Management
Even the shortest delays are costly on an established manufacturing line. Therefore, wherever your facilities are located, our experts are always within your reach to avoid downtime and to effectively support you throughout your operations remotely.
Mapvision Care programs provide not only verbal support via phone and email to your inquiries, but we roll up our sleeves when needed and work alongside your team to resolve any challenges you may face via the secure remote management capabilities embedded in your Mapvision Q-Series system within the access rights and permissions you grant our experts. Via remote management, we can for example eliminate any software issues or perform analysis on your production data to help you optimize your manufacturing processes.
Annual Maintenance
While your Mapvision Q-Series system is designed for absolute robustness that does not compromise measurement accuracy and precision even in the case of camera failures, an annual check-up and maintenance is essential just like any other measurement equipment.
Mapvision Care Standard and Extended programs provide an all-around annual maintenance service at your facilities by a visiting Mapvision expert; covering system calibration, certification, and measurement system capability checks to ensure absolute accuracy and precision for your Mapvision Q-Series System. The visiting expert also performs a thorough hardware cleaning and maintenance for all the optical, electrical, and mechanical systems.
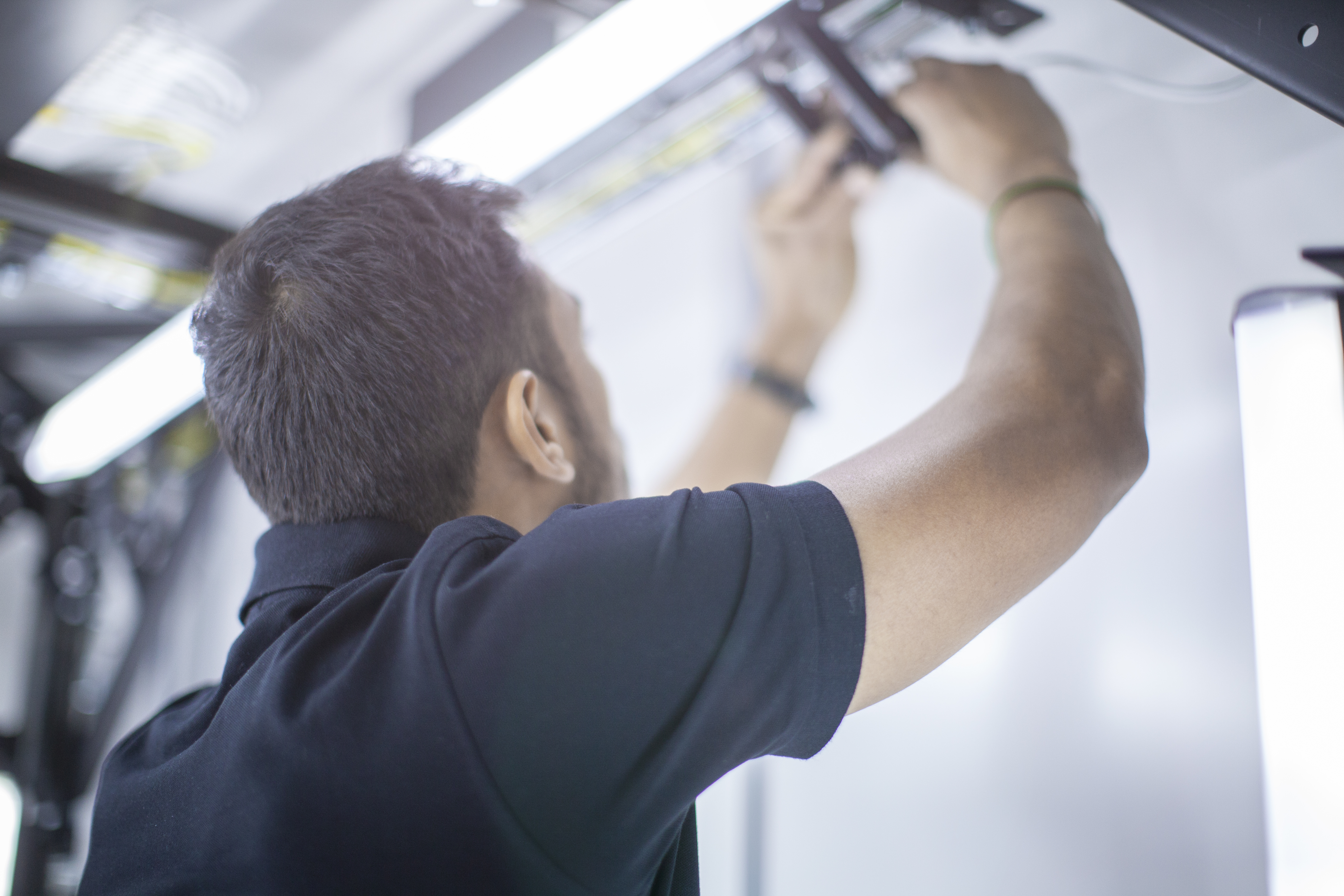
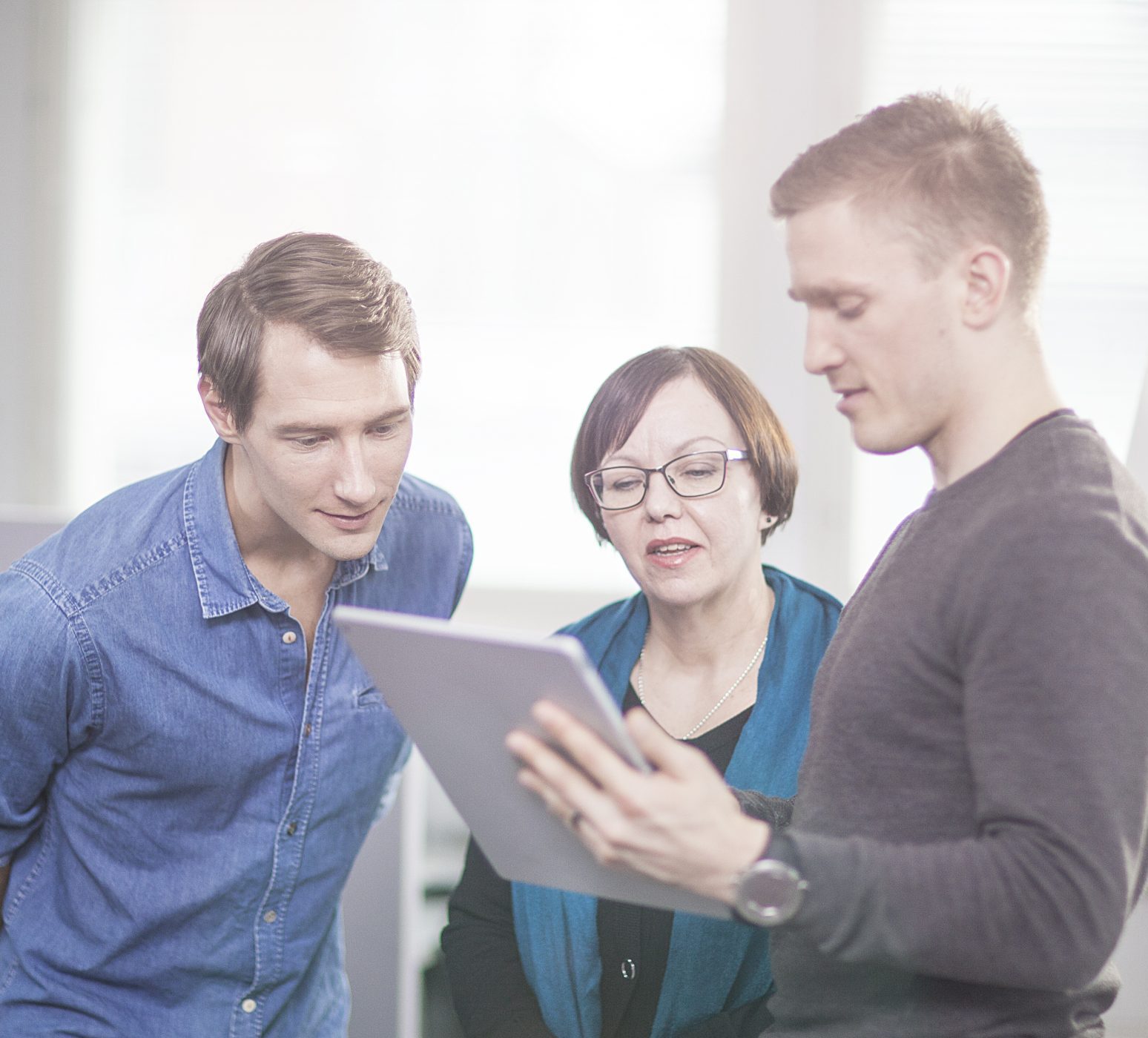
Engineering Changes & Feature Modifications
In a complex industry such as automotive, agility is a must-have and your service coverage needs to address that by providing you the flexibility, reducing any potential downtime, pacing production readiness, and cutting extra costs. The same rules apply for early-stage production lines and line set-up.
The Extended program provides the agility and responsiveness you need for your Mapvision Q-Series system to address engineering changes and feature modifications while avoiding extra costs. It covers, for example, adding/removing new features to be inspected, modifying the result output or deploying programming changes to introduce engineering changes to your in-line inspection process such as changing part geometry or visual appearance.
Program Comparison
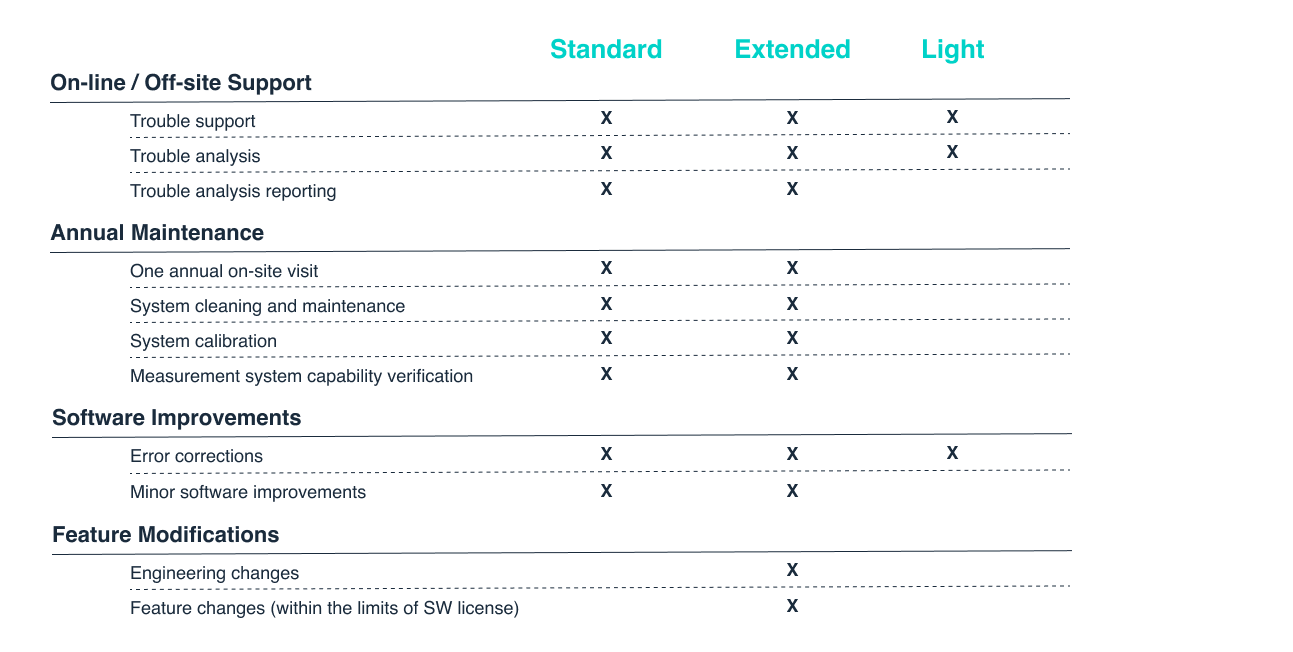